Kaneka Corp. is a chemical manufacturing company established in 1949 that provides solutions in the fields of chemicals, functional polymers, electronics, synthetic fibers, pharmaceuticals, medical devices, supplements and foods.
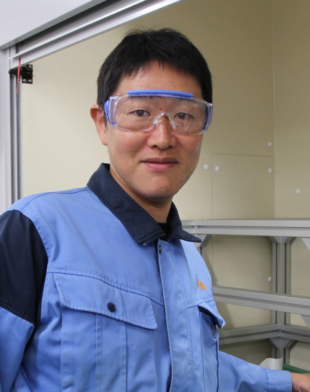
One of the environmental issues the company aims to address through its business is microplastic pollution. In a recent interview with The Japan Times, Shunsuke Sato, head of the CO2 Innovation Laboratory, talked about Green Planet, a biodegradable polymer that has the potential to help the environment while maintaining the convenience people enjoy from plastic.
Green Planet is a plant-based alternative to plastic that is made from vegetable oils and used cooking oil. It is used to replace plastic products such as straws, bags, cutlery, hotel amenities and films. Products made from Green Planet have physical properties similar to petroleum-derived plastics, and consumers may have encountered them in convenience stores or coffee shops without even realizing it.
Kaneka uses some vegetable oils that have been certified by the Roundtable on Sustainable Palm Oil as raw material, which attests to their sustainable sourcing of raw materials. The RSPO is a nonprofit organization dedicated to promoting sustainability and global standards across the palm oil supply chain. The company also maintains close ties with collectors of used cooking oil.
“The first sizable order of Green Planet products came from France over a decade ago, following the implementation of a new European Union regulation concerning the use of plastic materials. Supermarkets in France were obliged to identify alternative products that could replace fruit and vegetable bags made from conventional plastic,” Sato said. Kaneka responded to their needs by providing compostable bags made from Green Planet.
He added that plastic bags were lightweight and thin, which was ideal for weighing fruits and vegetables, but they could be easily torn, were only strong enough for a single use and could cause environmental harm if disposed of inadequately.
Foam packing materials pose similar problems, he said.
“Polystyrene foam is also lightweight and can be easily broken and carried away by the wind. This can result in a significant number of small pieces of foam ending up in the sea,” Sato said.
Green Planet, however, presents a potential solution to this problem as it can also be made into foam. “Recently, Sony has started to use Green Planet foam for packing some of its products,” he said.
Kaneka has also developed seedling pots using Green Planet. According to Sato, these pots don’t have to be removed when planting seedlings, providing not only convenience, but also protection as roots are often damaged when attempting to remove plants from pots.
The use of Green Planet in manufacturing coffee capsules and pods is also gaining traction in Europe.
“Composting has become a standard practice in many European countries, with separate trash cans for different types of garbage, including compostable, burnable, nonburnable and recyclable materials in public spaces,” he explained, noting that coffee capsules and pods made of Green Planet can be composted directly, eliminating the need to separate the grounds from the containers or burn them with the wet contents inside. “Our objective is to address the issue of ‘not being able to separate’ by utilizing a 100% biodegradable material,” he said.
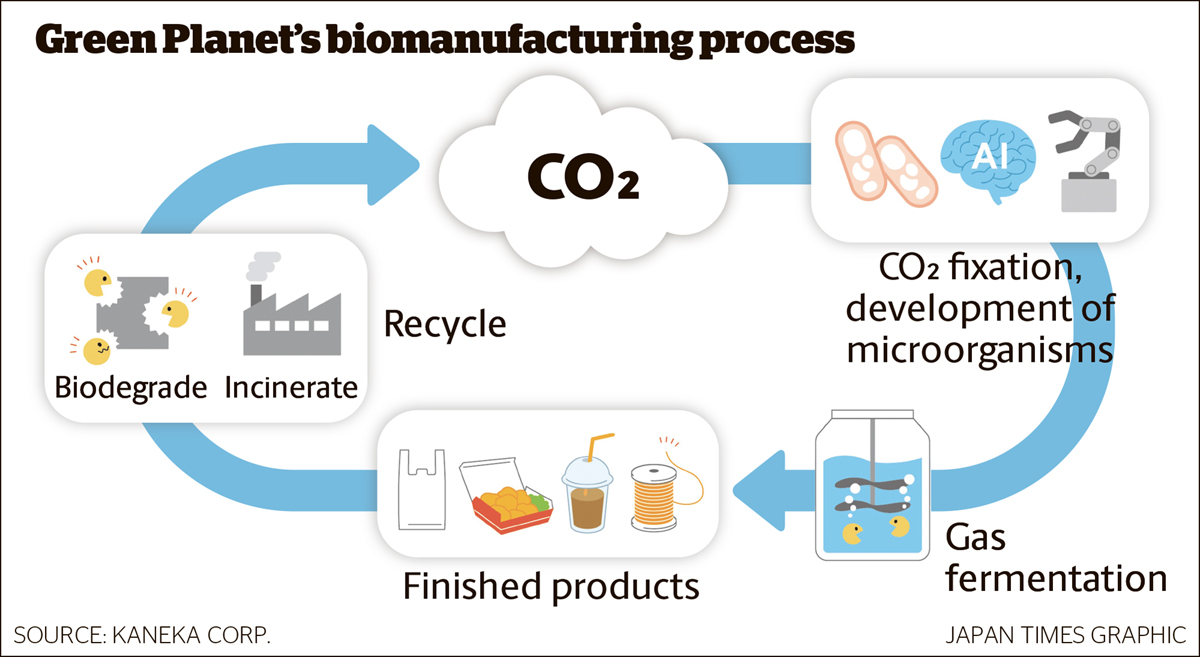
The biodegradation rate is affected by various factors, including surface area, temperature, available nutrients and number of microorganisms.
“Maintaining the material in an environment where microorganisms are active will accelerate the biodegradation process,” Sato explained. Green Planet’s high degradability, coupled with the company’s expertise in state-of-the-art synthetic biology, molding and processing technologies, allows it to be made into a variety of shapes suitable for applications across the globe.
In fact, Green Planet is already being used extensively in the EU, the United States and Japan.
“More than 50% of Green Planet products are exported. We are anticipating an increase in its international sales, particularly in countries such as the United States, where there is a significant demand for plastics for packaging snacks and fast food,” Sato said.
“Numerous products are used and discarded without any awareness of their plastic content,” Sato explained. For instance, the insides of paper cups are typically covered with plastic waterproof films. Kaneka aims to expand the use of Green Planet to replace these unrecognized plastic elements and items.
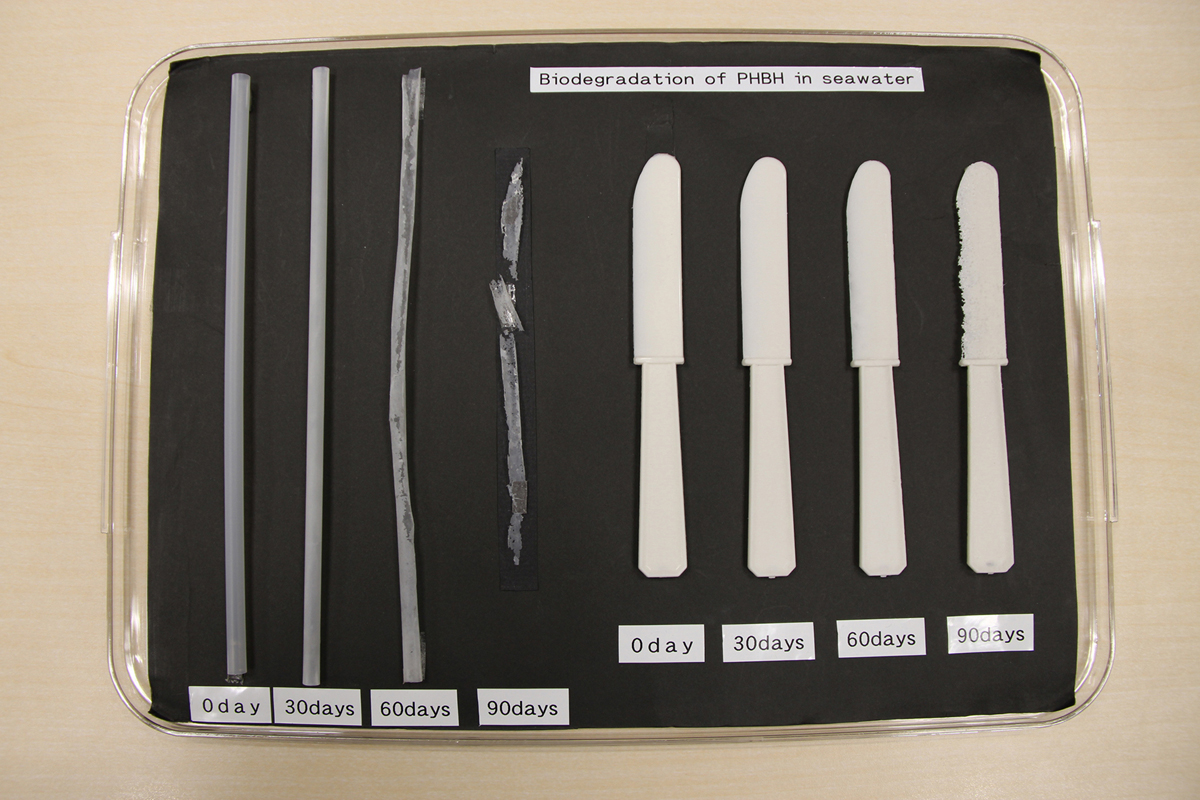
At present, eco-friendly products are gaining ground in shopping bags, followed by straws and cutlery. The company’s objective is to apply Green Planet to a broader range of packaging solutions for foods and beverages.
“The item we have yet to trial with the highest priority is PET (polyethylene terephthalate) bottles. A vast number of PET bottles are manufactured and utilized globally, becoming a primary contributor to marine plastic waste. We are aiming to replace PET bottles with those made from Green Planet,” Sato said.
The company initiated the development of biodegradable polymers in the early 1990s. In those days, the term “marine plastic waste” was not yet common. The environmental issues of concern at the time were different from today’s.
In the ’90s, waste was typically either incinerated or used for landfill. But it was the growing concern over the environmental impact of landfill sites that caught the company’s attention. “That was the initial motivation for our research and development of biodegradable polymers,” Sato explained.
The focus of the debate, however, soon shifted to the climate threat posed by the carbon dioxide from the incinerators. So the company is taking on that challenge via Green Planet as well. “Our current research is focused on the use of carbon dioxide as a raw material for Green Planet production,” Sato said.
This is done through microorganisms known as hydrogen-oxidizing bacteria, which can transform carbon dioxide into organic substances.
“These bacteria have existed on Earth since microorganisms first appeared, which is why our planet is now home to a vast array of organic substances,” Sato explained. Kaneka is attempting to extract and use materials contained in these substances to make Green Planet.
“This technology will make Green Planet not only biodegradable, but also ‘circular’ in terms of sustainable production. This is because the carbon dioxide emitted during the disposal of used Green Planet products can be fixed during the manufacturing process, returning the carbon to an organic state,” he said.
Sato revealed the technology has proven viable at the experimental level and that the next phase will see it applied to industrial production. He highlighted that the primary challenge is to develop a stable method for cultivating a large quantity of hydrogen-oxidizing bacteria in a hydrogen gas environment.
“It is also essential that we work closely with hydrogen gas providers to establish a reliable value chain in a market where the technology to develop a hydrogen supply infrastructure is still evolving,” he said. Despite the challenges, the company is targeting commercialization of carbon dioxide-derived Green Planet by 2030.
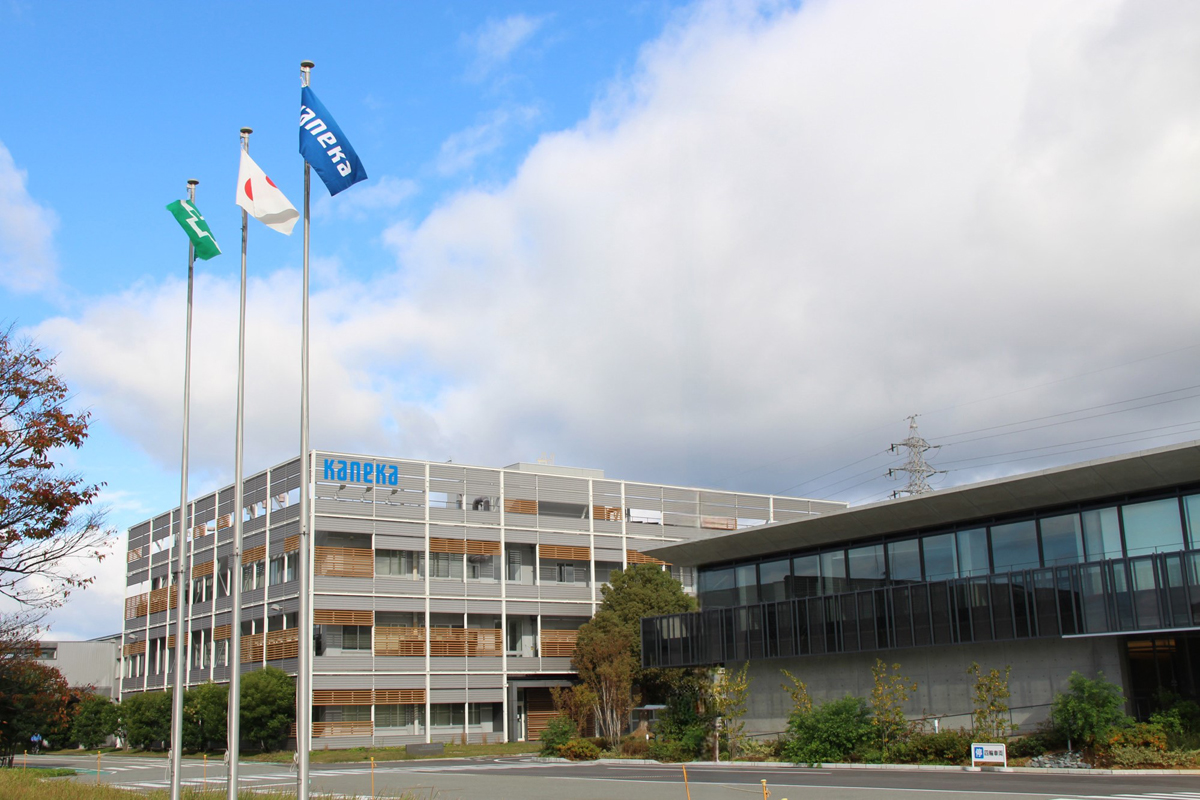
The company’s efforts to evolve Green Planet will not end there. Sato explained that Kaneka will continue to explore new substances from which to produce Green Planet, with a view to diversifying the raw materials used and ensuring stable production. “I believe there are numerous other potential raw materials that could be utilized, as long as they can be metabolized by microorganisms and are fossil-free. The diversification of materials, including the use of carbon dioxide, will help avoid the depletion of raw materials,” he said.
“We are seeking solutions to the question of what we should use to create the everyday goods people use to achieve higher levels of sustainability in society,” Sato said. While going back to pre-Industrial Revolution lifestyles is one way to achieve sustainability, he believes it is necessary for people to realize a “circulatory society” by using the science and technology that humanity has worked so hard to advance. “This is also our responsibility as a chemical manufacturing company,” he said.
This article is sponsored by Kaneka Corp. Visit https://www.kaneka.co.jp/en/solutions/phbh/index.html for more information.