While the textile and apparel industry provides products that enhance people’s lives with color and style, it also has a significant environmental impact. One Japanese startup is gaining recognition at home and abroad for its innovative solutions to this problem from the perspective of basic materials.
Bioworks is involved in the research and development of the environmentally friendly material PlaX, as well as the manufacture and sale of yarn using it. In a recent interview with The Japan Times, Representative Director and CEO Koji Sakamoto provided insights into the challenges currently facing the industry and outlined how Bioworks is addressing them.
Sakamoto noted that the fashion industry is widely regarded as the world’s second-most-polluting industry. “There are three key reasons for this. Firstly, it is one of the largest emitters of greenhouse gases globally. Secondly, the industry uses a considerable amount of water, equivalent to the amount used by approximately 5 million people on an annual basis. Thirdly, it is a significant contributor to the issue of microplastics,” he said.
He added that about 70% of the fibers used in everyday fabric items, including clothing and bed linens, are synthetics. “Dust and lint from chemical synthetic fibers are carried into the ocean through sewage. It is estimated that approximately one-third of the microplastics present in the ocean originate from synthetic fibers.”
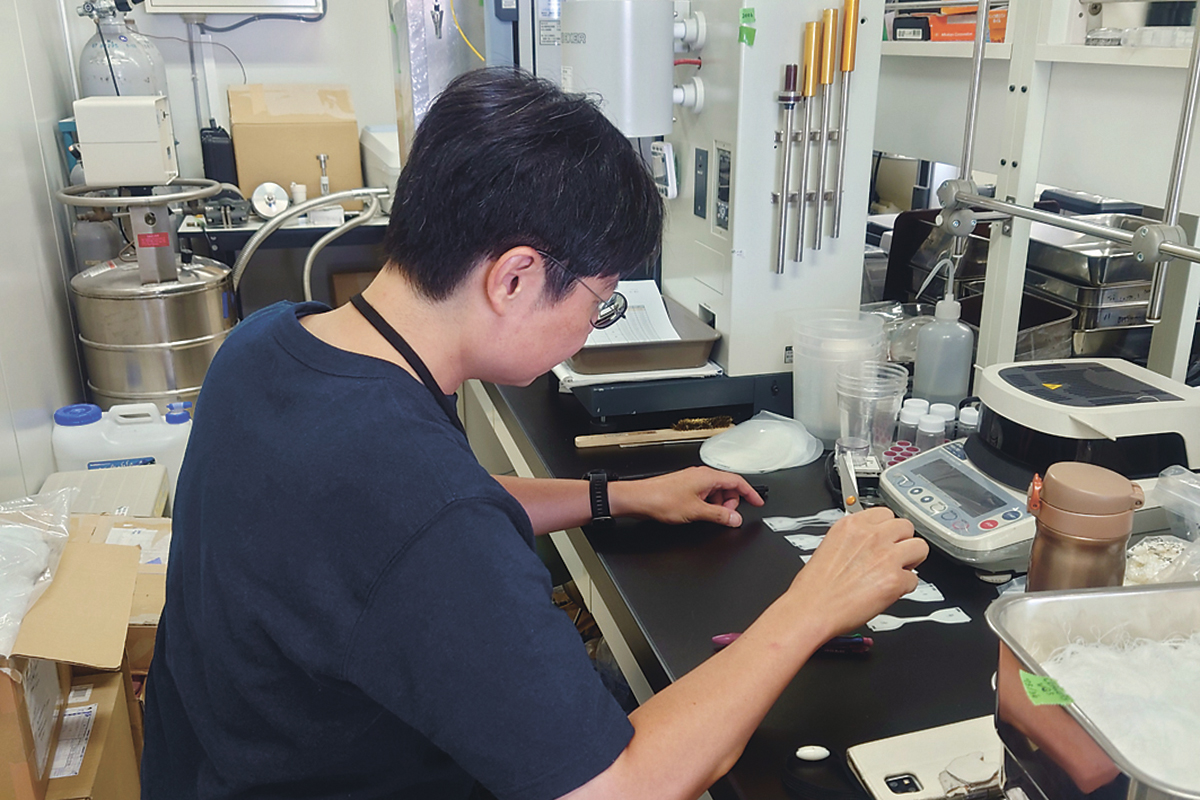
Bioworks was founded with a focus on the research and development of materials, with sustainability in mind. However, textiles were not its initial product line.
In 2015, the company was established with technological expertise in the production of bioplastic products, including food and drink containers made from PlaX, a polylactic acid material with improved heat resistance and durability. PlaX is made from lactic acid produced by the fermentation of starch and sugar derived from plants such as sugarcane and corn. It is thus biodegradable. “The biodegradation process can be accelerated by maintaining a compost-like environment at high temperatures and humidity. Even if it is incinerated, the carbon dioxide released when it is burned can be offset by the carbon dioxide the plants absorbed while they grew,” Sakamoto explained.
In 2020, looking for new ways to use PlaX, the company identified the potential for making fibers from it. “In 2021, we shifted our focus to manufacturing yarns, which resulted in the invention of PlaX fiber. We commenced mass production at the end of 2022, and PlaX has been used to manufacture apparel products since 2023,” Saka-moto said.
The textile and apparel industry was swift to recognize the potential of this innovation. In 2024, about 40 brands opted to utilize PlaX. Roughly 30 of those, including the noted outdoor brand White Mountaineering and the British brand Margaret Howell, already offer products that contain PlaX. Bioworks has its own brand, called Bio, that offers towels and T-shirts made from PlaX.
“It is estimated that approximately 90% of chemical synthetic fibers, which represent about 60% of all fibers used for manufacturing daily items, is polyester. Despite its negative environmental impact, polyester is widely used for various products, including sports and outdoor items, due to its strength and quick-drying characteristics,” Sakamoto said.
Until the introduction of PlaX by Bioworks, there were few options of environmentally friendly substitute for polyester because achieving similar features while also ensuring environmental sustainability was technically challenging.
The manufacturing process for PlaX is also similar to that of polyester, and so it is possible to simply adjust settings at standard yarn factories, eliminating the need for new factories.
“We do not own any manufacturing facilities. We provide our material to existing polyester yarn manufacturers, collaborate with them to identify the optimal machine settings for the material, and conduct repeated testing until we achieve the desired results,” Sakamoto explained.
The company is extending this collaboration overseas. “We already partner with a factory in Taiwan that produces PlaX yarns. We plan to expand our global reach by working with plants in Thailand and other locations worldwide,” he said.
PlaX yarns can be sold to fabric makers, and the resulting fabric goes to sewing plants the usual way. Like polyester, PlaX can be easily blended with other materials, including cotton, wool and even cellulose, a relatively new, nature-based material. “We are committed to further experimenting with different blending ratios in order to pursue specific functions and textures for various purposes,” Sakamoto said.
Sakamoto is confident that there is vast potential for diverse collaborations with existing players thanks to the polyester-like versatility and ease of handling of PlaX, and because there is no need for new machines and facilities to make PlaX yarns and fabrics. The greater the use of this material, the greater the positive impact that the industry can collectively have on the environment.
Bioworks is seeking new opportunities to connect with fabric manufacturers and fashion brands on a global scale. To this end, it has been participating in the Premiere Vision in Paris, one of the largest and most prestigious exhibitions for fashion manufacturing worldwide, since July 2023. “A significant number of visitors from companies and factories looking for innovative, environmentally friendly materials were drawn to our booth. We have now established a pool of potential customers abroad and are continuing our efforts to enhance our collaborations with international brands. We will be able to see some items that use PlaX being sold in the global fashion market from next spring,” Sakamoto said.
In response to growing concerns over the impact of microplastics on marine ecosystems, Bioworks is exploring the potential of utilizing PlaX in the manufacture of fishing nets, which are often identified as a significant source of ocean pollution. The idea originated with companies in the fishing industry that had heard about PlaX. “Our goal is to meet their requirements by enhancing the strength of PlaX fibers,” Sakamoto said.
Another noteworthy attribute of PlaX is its exceptional antibacterial and anti-odor properties. Its antibacterial properties have been proven effective against some of the major bacteria that cause infections, including Staphylococcus aureus, Escherichia coli, Klebsiella pneumoniae and Moraxella bacteria. “Test results demonstrate that a towel containing 20% PlaX exhibits a strong antibacterial effect, making it an appropriate material for use in underwear, baby clothes and bedding. We are currently selling select items,” Sakamoto said.
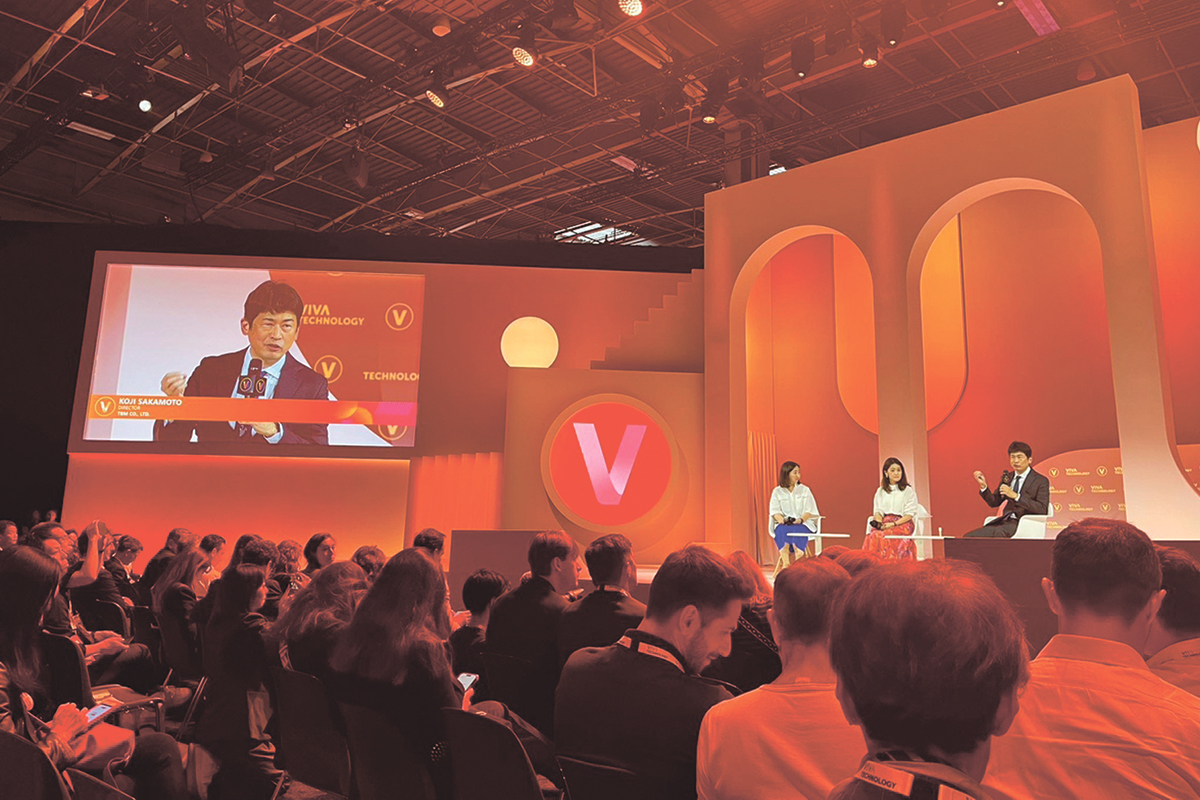
Bioworks’ commitment extends beyond the manufacture and sale of PlaX. The company is also concerned with the fate of the material after it has been used. “By collecting used items that contain PlaX, extracting it and turning it back into a material, we can minimize the use of raw materials such as sugarcane and corn,” Sakamoto said. This is a critical way of thinking for conserving resources utilized in agricultural production, curbing agriculture-related carbon dioxide emissions and avoiding potential conflicts with food production.
He added that the chemical recycling method currently under development will facilitate high-quality recycling. “Although we are still in the experimental phase, our goal is to establish a method that enables 100% recycling without the need to add any virgin materials, leveraging on the highly recyclable characteristic of polylactic acid,” he said.
The company is also working to ensure that the entire production process, from raw materials to finished products, is fully traceable. “Our goal is to disclose all data and processes to maintain transparency by engaging all stakeholders, including raw material producers and fashion brands selling products containing PlaX,” Sakamoto said.
This is a significant step to align with evolving consumer attitudes toward fashion, which extend beyond aesthetic and functional considerations to encompass the origins and production methods of the products they purchase.
To guarantee the credibility of the entire value chain, the company is committed to making various efforts, including reducing and monitoring greenhouse gas emissions, guaranteeing that no harmful substances are used and ensuring that work environments are safe and desirable throughout the value chain.
So far, a life-cycle assessment analysis has revealed that PlaX emits 41% less carbon dioxide during its manufacturing process than polyester and uses 90% less water than cotton. “Regarding the raw material, we are procuring polylactic acid from a plant in Thailand that belongs to Total Corbion, a joint venture between Total Energy, a major energy company in France, and Corbion, a Dutch company that is a leader in polylactic acid technologies,” Sakamoto said. He noted that the plant has been certified by an international organization for its working environment, use of agricultural chemicals and other factors.
Bioworks looks set to become a leading innovator in the fashion industry, driving the transition toward greater sustainability and letting consumers enjoy more sustainable fashion experiences.
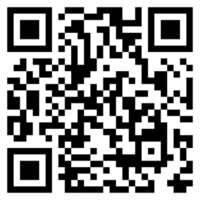
