Tsubame-Sanjo, which is centered on the cities of Tsubame and Sanjo in Niigata Prefecture, is a fertile, rice-producing region on the Sea of Japan coast. But the area is also well known as a metalworking powerhouse that has carried on for over 400 years since the Edo Period (1603 to 1868).
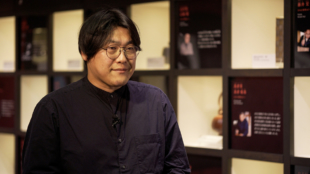
Firms ranging from small factories to big enterprises form a major industrial cluster in this area. They produce cutting tools, tableware, golf clubheads and other products based on metal-processing technologies developed by local craftspeople.
An expert on this area is Yusuke Saito, a curator at the Tsubame Industrial Materials Museum.
“While traditional metal-processing technology from 200 years ago still thrives today, we can also witness cutting-edge technology here,” Saito said. “There is no other area like this in the world, where old and new industries coexist today. And what is amazing is that many businesses born in this area are notable in their fields.”
For example, Yamazaki Kinzoku Kogyo Co. became the first company outside Sweden in 1991 to provide high-quality cutlery for the tables at the Nobel Prize winners’ banquet, while Endo Manufacturing Co. supplies clubheads to world-famous golf brands used by the world’s top professional golfers.
But truly unique to the local industry is a system called open factory. Under this system, visitors can stop by various factories without a reservation and closely observe the workers and artisans there.
One of the first to embrace the open factory concept was Suwada Blacksmith Works Inc., a Sanjo-based cutting tool and nail nipper maker founded in 1926.
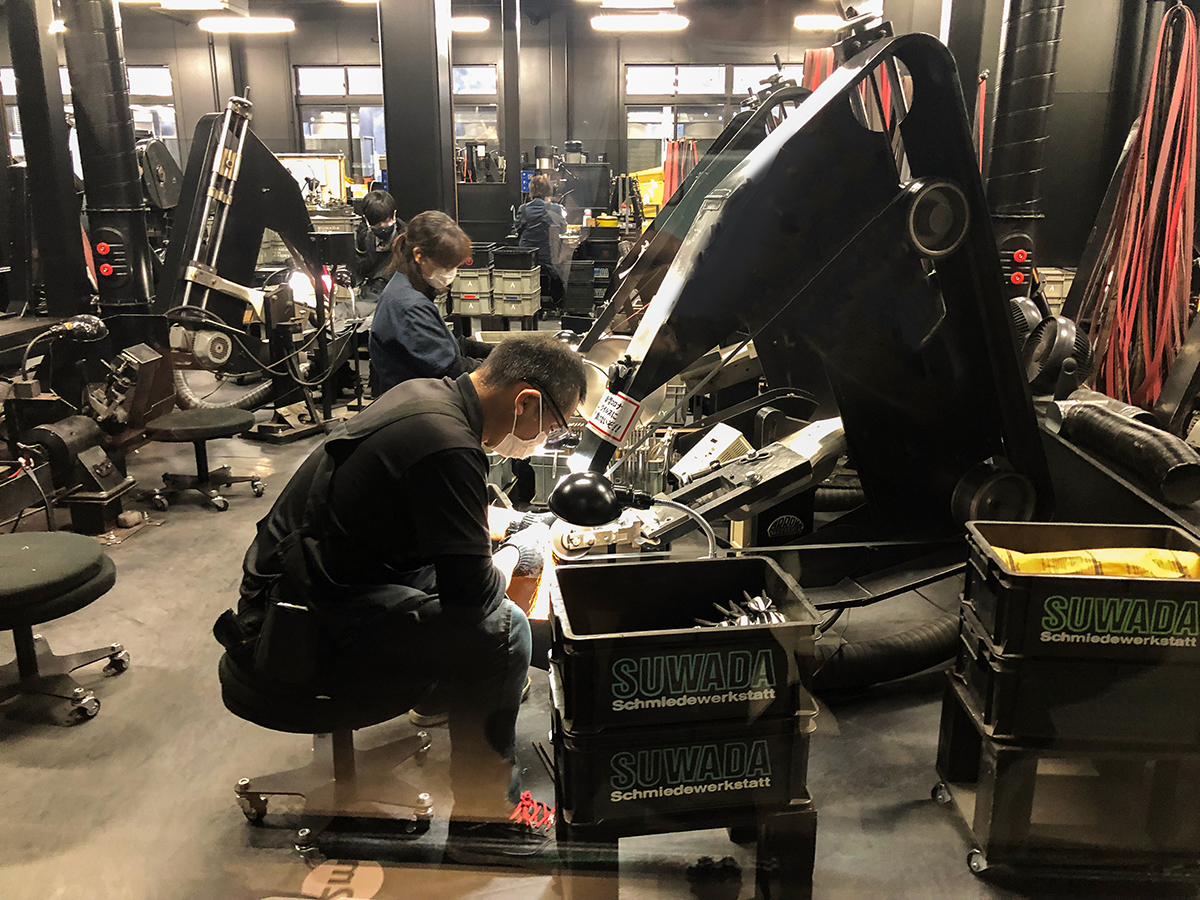
Suwada’s nail nippers, which are similar to pliers and used to cut finger and toe nails, are fully handcrafted individually through the forging, grinding and finishing processes. Their blades are gently curved to match nail shapes and can cut even thick or abnormal nails, making them popular with professionals at nail salons and medical clinics around the world, according to the company. Suwada is also the world’s only manufacturer of bonsai shears.
“Because we continue to make our products with traditional techniques, our factories used to attract some 500 visitors every year. But when the number reached around 1,000 people, we thought we could no longer guide visitors around. So in 2011, we decided to let visitors watch our manufacturing process for themselves while our craftspeople worked,” said Tomoyuki Kobayashi, president of Suwada. “We value quality, and our artisans make our products without compromise. I am sure visitors can sense that by watching them closely.”
Kobayashi said that to survive in this competitive market, the skills and experience of craftspeople must constantly be developed, and young men and women are taking on such responsibilities at his company.
Based on the open factory concept, Kobayashi and other like-minded business leaders founded the Tsubame-Sanjo Factory Festival in 2013. During the festival, people can tour different participating factories to learn about the world of manufacturing firsthand. In that first year, 54 companies participated in the festival. By 2019, that number had more than doubled to 113. As many as 56,000 people have attended the festival so far.
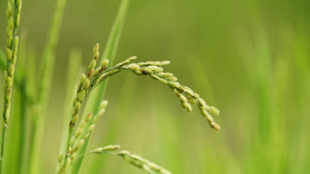
Because of COVID-19, instead of the festival, an exhibition titled “Tsubame-Sanjo Factory Museum” was held at a disused factory this November. Local industrial products and the tools used to make them were put on display. Visitors were also shown films of the products being made.
Gyokusendo is another company that continues to follow traditional methods to make hand-hammered metalware, such as teapots, kettles and other types of serving vessels. Since its founding in 1816, Gyokusendo has passed down its tsuiki copperware techniques to generations of craftspeople, including those working today. During the Meiji Period (1868 to 1912), its artistically decorated copperware was displayed at various international expos overseas, according to the company.
The company can produce eight different colors with its oxidation methods. It’s an original coloring technique that was developed over seven generations.
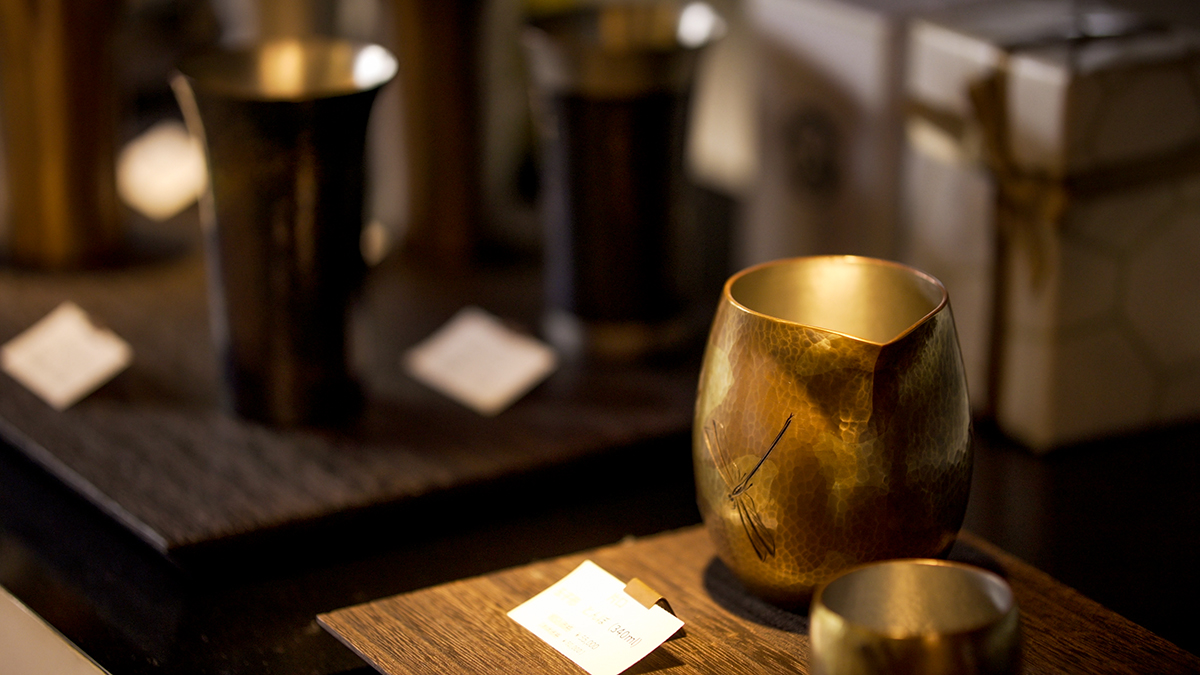
Ritsu Yamada, general manager of Gyokusendo, said that the company has been hit hard several times throughout its long history but has always managed to come through.
“During the war, we suffered from a shortage of copper, and most of the craftspeople were conscripted to fight in the war,” Yamada explained. “Our factory was also reportedly turned into a weapons factory then.” He added that the collapse of Japan’s bubble economy in the early 1990s and the COVID-19 pandemic also triggered sharp drops in sales.
Because many overseas customers, predominantly from China and Europe, cannot visit Japan right now, the company is currently reviewing new ways to sell its products, he said.
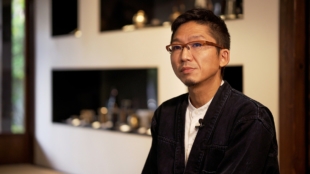
“Before the pandemic, we weren’t really interested in selling via the internet,” he said. “Since we cannot meet face-to-face with overseas customers now, we are exploring ways to enable our customers to understand the quality of our products online.”
Still, Gyokusendo is a popular destination for visitors to Tsubame. They can watch the artists do their handiwork at the workshop despite the pandemic. The workshop is full of young artists, many of whom are art school graduates.
Yamada said that in recent years, 40 to 50 young people apply to work at Gyokusendo every year. They enjoy learning traditional metalworking techniques, and some have even moved to Tsubame from outside Niigata Prefecture to work there.
“The open factory concept is not just about selling our products; it’s also meant to interest young people in becoming the craftsmen who will pass on this technique to future generations,” he said.
Tsubame Museum’s Saito said the fact that young people are drawn to work at the area’s factories and workshops is a very promising sign for local industries.
“I think being young could be a big advantage because they can form a long-lasting partnership with other businesses outside this area,” Saito said.
Saito said that the techniques of hammering metal, shaping it and cutting it have remained mostly unchanged since the Edo Period.
“But a variety of products have been created to meet the needs of the times and presented to the world in different forms,” he said. “It is the result of our efforts to keep up with the times that has made Tsubame what it is today.”
This story was produced by Pacific Bridge Media & Consulting.