Masaki Sukegawa has been crafting golf clubs for more than 18 years in his workshop at Endo Manufacturing Co. It’s his job to turn lumps of metal into master models for clubheads used by some of the world’s top professional golfers, as well as weekend duffers.
It takes about a week of delicate grinding and filing to shape the head of an iron. Sukegawa says the entire process of completing a master model takes more than a month.
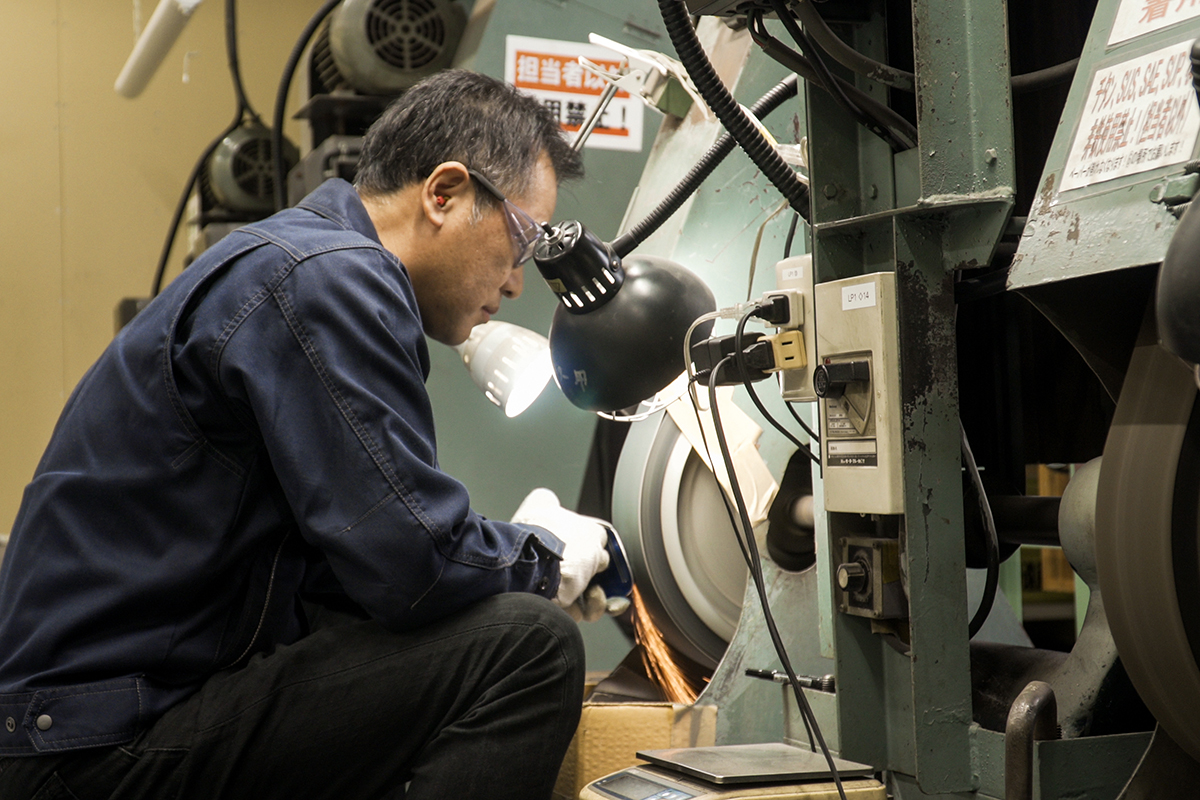
Endo is based in Tsubame, Niigata Prefecture, a traditional center of metalworking. Sukegawa’s official title is assistant manager and meister of master model grinding. He works in the Golf Department’s Product Design and Development Division. He is one of only two clubhead makers at the company with the title of meister.
Professional golfers frequently visit his workshop to order their clubs. The meisters make fine adjustments based on client requests. For instance, they might be asked to fashion a slightly smaller clubface, or make a certain part rounder.
“When I actually see professional golfers on TV win a tournament with our golf clubs, I feel delighted and I find my job rewarding,” Sukegawa said in front of a wall decorated with the framed autographs of pro golfers who are clients.
But the company is not well known to the public. As an original equipment manufacturer, Endo’s products are sold under other sports brand names.
Endo began in 1950 as a small factory turning out screwdrivers and sewing machine needles. Thanks to its advanced metal-processing technologies, especially in forging, it has grown to have a variety of businesses under its wing beyond clubheads. Other products include auto and aircraft engine parts, medical devices and office automation equipment.
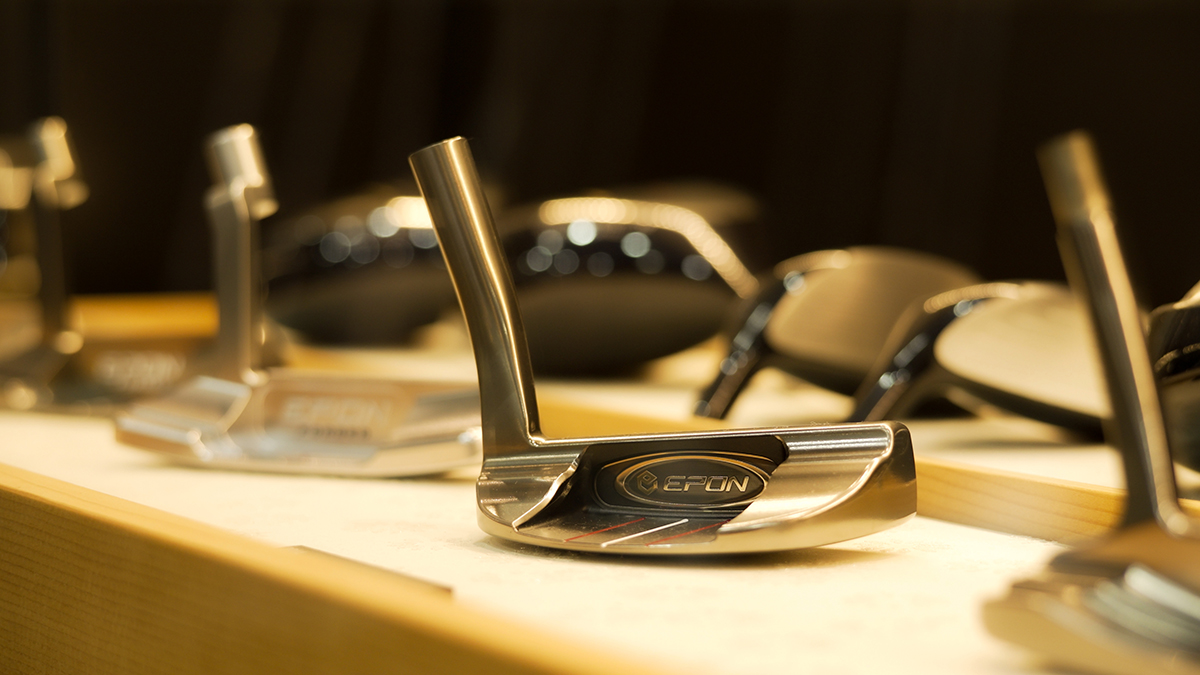
The clubhead business in particular has taken off during the pandemic, with the rise in popularity of golf. Endo’s original golf equipment brand, Epon Golf, has also gained ground among top golfers in Japan and abroad.
Endo’s production of clubheads so far this year has significantly increased compared with last year, according to Toshimitsu Oyamatsu, general manager of the company’s Golf Business Department.
Oyamatsu said the company’s clubheads are forged, not cast, and all of the work is done in-house. This means that Endo, one of the few clubhead makers in Japan, can swiftly respond to customers’ requests.
In forging, red-hot metals are pounded into shape.
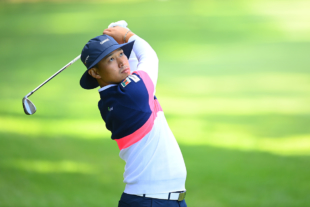
“By hitting the metal again and again, it becomes strong. Our forging technology significantly enhances the physical characteristics of the metal such as its strength and flexibility,” he said. “When playing golf, it also brings a comfortable feel at impact.”
While continuing to supply clubheads to major sports brands around the world, the company established Epon Golf in 1977. Last year, Epon signed its first sponsorship deal with professional golfer Naoto Nakanishi. The 33-year-old actively promotes golf on social media. In 2019, Nakanishi was 64th on the list of prize money winners in Japan. This year he has risen to 46th.
“Nakanishi often calls me and tells me what kind of clubheads he wants, and I also propose some changes,” clubhead craftsman Sukegawa said. “Based on our conversations, we come up with better clubheads to improve his performance. We are in constant communication.”
Endo President Taishi Watabe was moved to support Nakanishi by his enthusiasm to revitalize men’s professional golf in Japan. Watabe felt Japanese professional golf lacked superstars like Ryo Ishikawa, who triggered a golf boom in Japan a decade ago.
Though Endo’s golf business is thriving, Watabe is eyeing overseas markets, judging that the Japanese market is near its peak.
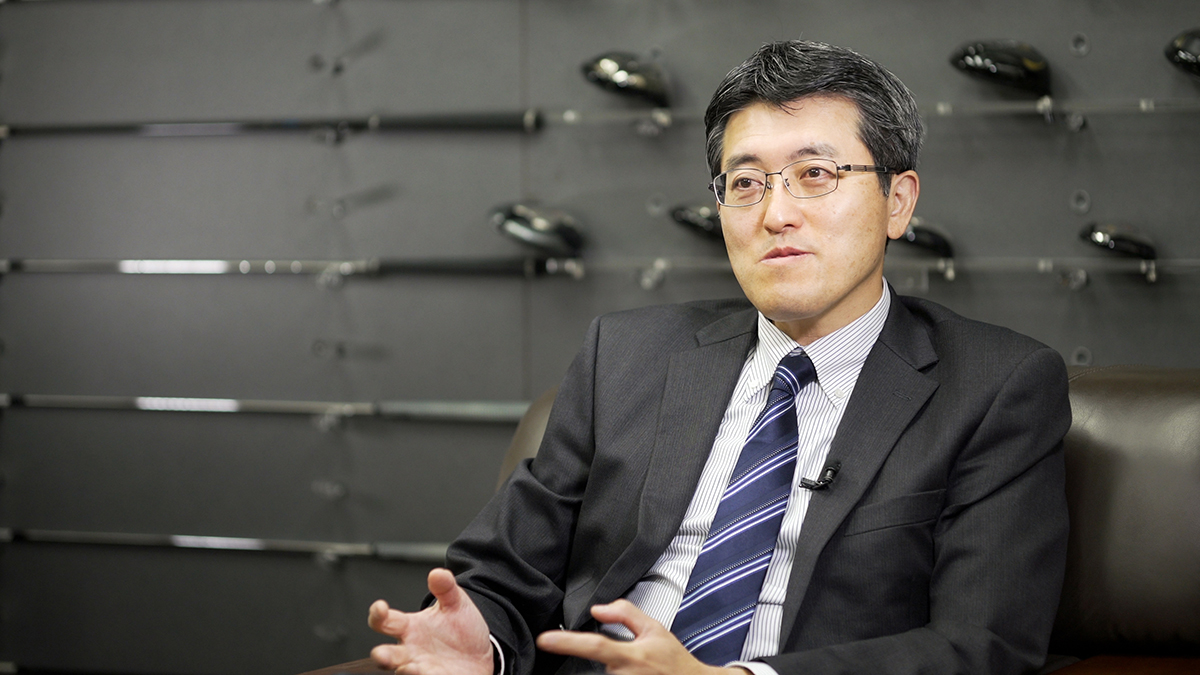
“The number of golfers might have temporarily jumped during the pandemic, but in the long term, it will gradually decline because of the aging population in Japan,” Watabe said, adding that the company is currently negotiating deals with U.S. brands.
The company’s other businesses have also developed over the years. For example, medical devices posted 4% annual increases before the pandemic.
Endo entered the medical field in 2009. It uses its precision forging technology to produce orthopedic implants, such as artificial hips and knees.
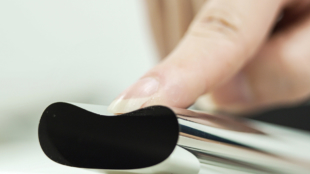
Another product that it boasts of is metal sleeves, which have been developed using its processing technology for ultrathin metal. According to the company, the manufacturing of metal tubes normally involves welding, extracting and cutting.
But by using its proprietary technology, the company can produce ultrathin seamless pipes that can’t be made with conventional technology. They are currently used in copiers and printers.
“We could develop this technology because of the local metal-processing technology nurtured in this area,” said Katsutoshi Maruyama, director of the company’s metal sleeve business.
Maruyama said by using this technology, ultrathin seamless pipes can be produced not only in stainless steel, but also in other metals, such as nickel and titanium alloys.
The company is looking at other markets where its unique technology can be employed.
“People still don’t know about metal sleeve technology, and it is essential to let them know and cultivate demand both in Japan and abroad,” he said.
Watabe said the challenge for Endo is to expand into new fields, such as medicine and aeronautics, while continuing to make inroads in existing markets.
He said that Endo will continue to evolve as it has in the past. When the market for sewing machine parts dried up, the company switched to making kitchen utensils.
“As markets mature and decline, we’ve always managed to make good transitions to new business sectors,” Watabe said. “In the next 20 to 30 years, we hope to continue in this spirit of overcoming challenges that we have developed over years.”
This story was produced by Pacific Bridge Media & Consulting.