In Japan, most polyethylene terephthalate (PET) bottles are collected and recycled after use. According to The Council for PET Bottle Recycling, Japan’s collection rate was 92.2 percent and the country recycled 84.8 percent in fiscal 2017.
According to the council, Europe in comparison as a whole recycled 41.8 percent of plastic bottles and the U.S. 20.9 percent.
However, Suntory Holdings Ltd., a global beverage producer based in Japan, has recently announced a higher and more specific target; that is, to replace all of the PET bottles they use for their beverages with ones made of 100 percent recycled and bio-derived PET by 2030.
“As a major user of PET, we must lead the world in improving the way we make, use and recycle PET,” said Takeshi Niinami, president and chief executive officer of Suntory Holdings.
According to Suntory, about 99 percent of the plastic that the company uses on a global scale are for beverages. Approximately 80 percent of the plastic is made of PET.
Suntory continues to engage in international environmental conservation and education to preserve nature and resources for future generations. Tackling the challenge of PET recycling was a natural choice for the company in a time where plastic waste is a major issue.
Plastic did not start out being perceived as inherently evil. Although the material has contributed to the modernization of food hygiene, portability and packaging, its environmental drawbacks are much clearer today.
Suntory believes clever application of plastic is better than eliminating it altogether. But, in that case, how can society be smarter about plastic usage and recycling?
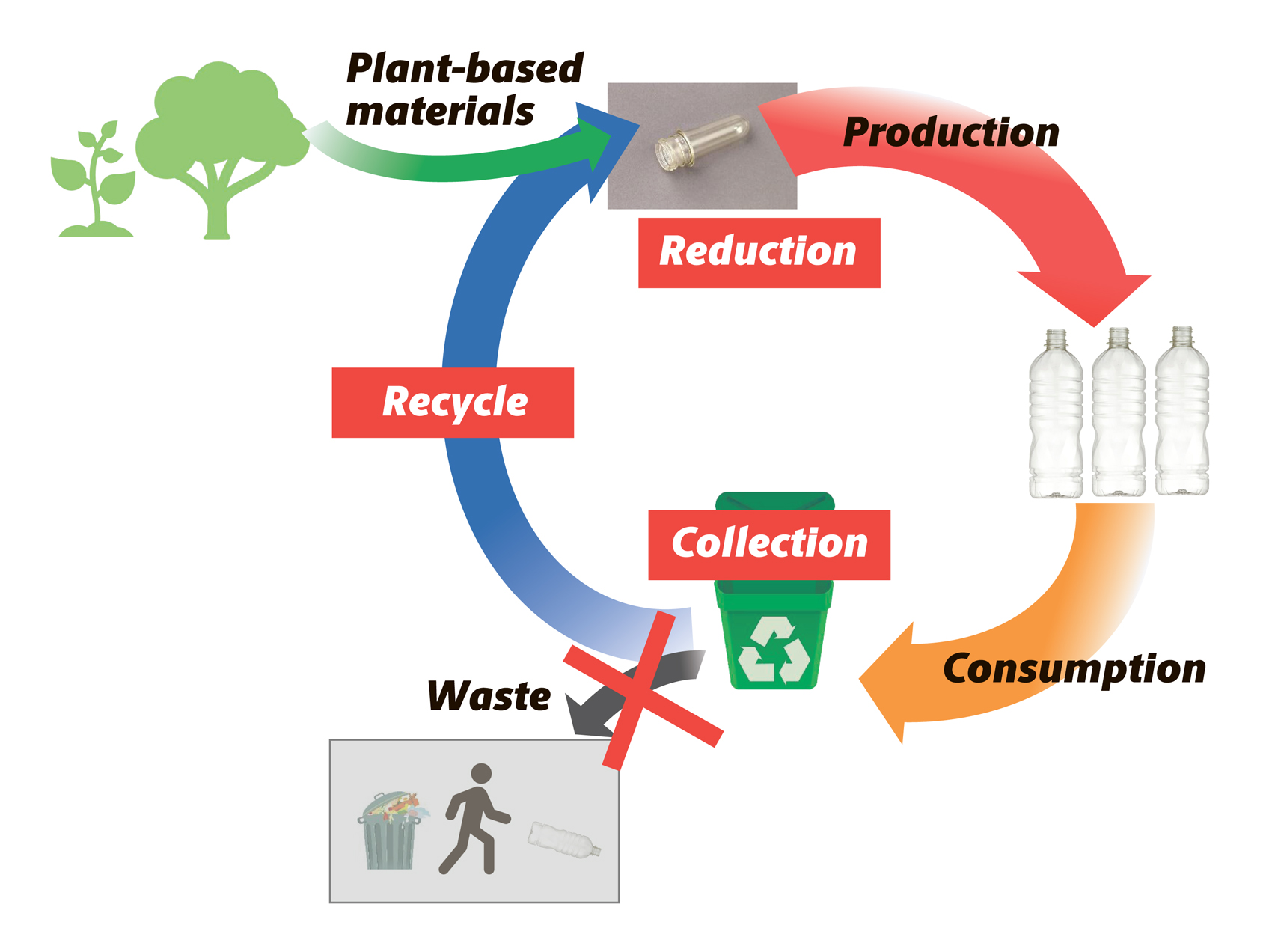
The company said, “It is not just recycling, but recycling with less carbon emissions.” The recycling rate is already high in Japan, but the fact that most people may be unaware of is that most of the collected used PET bottles are recycled and become products that are not PET bottles.
According to The Council for PET Bottle Recycling, the amount of PET resin used for manufacturing PET bottles was about 700,000 tons in 2017. However, only 61,300 tons, about 10 percent, is used for making recycled PET bottles, the council said.
The process of used PET bottles to make recycled PET bottles has been technically more difficult. However, petroleum, the main ingredient of the conventional PET, will continue to be exploited if new technologies for bottle-to-bottle recycling are not developed. This is what Suntory is dedicated to.
Suntory’s 2R+B strategy is built around reducing plastics and recycling them while utilizing bio-based, rather than petroleum, materials. This means making bottles thinner and caps shallower to cut down on the amount of PET used, developing petroleum-free PET and processing used bottles with mechanical recycling techniques when making new ones.
There are two ways of recycling PET bottles — one is chemical recycling and the other is mechanical recycling. Chemical recycling requires a lot of energy as it breaks down PET to a molecular level, while mechanical recycling can handle bigger pieces of PET at the molecular level; this is better in terms of energy consumption, but the bottles need to be cleaned thoroughly before the recycling process begins.
Collecting clean bottles has always been a challenge.
“Those collected by local governments are relatively clean. We will continue to collaborate with local governments, distribution channels and other stakeholders to boost the collection of clean bottles suitable for bottle-to-bottle recycling,” noted Kenji Naiki, deputy senior general manager of the Corporate Sustainability Division.
This is harder in countries where collection of used PET bottles has not progressed as much compared to Japan. For example, the collection rate in Europe is two-thirds that of Japan, according to The Council for PET Bottle Recycling. In some countries in Southeast Asia, there is no collection system in place.
“Forty-one percent of our PET-bottled products are sold in Japan, 35 percent are distributed to some of the ASEAN (Association of Southeast Asian Nations) countries and 15 percent to Europe. We need to act globally,” Naiki said.
Suntory as a whole hopes to address this. Niinami stressed that the company will take initiative in facilitating collaboration among other beverage makers and the distribution industry to support and encourage the government to introduce a collection system in some of the countries where Suntory’s products are sold.
“ASEAN countries have close ties with the government of Japan, so we will also approach the government to encourage intergovernmental cooperation in introducing and enhancing the collection system,” Niinami said. “There are no borders in environmental issues. Cross-border efforts need to be made based on the cooperation among different countries to address the issues. Global enterprises should take the initiative.”
Suntory’s efforts toward achieving its 2030 target in Japan will likely serve as a case model for other countries that consume its products.
The company has further developed the mechanical recycling system to include what it calls “FtoP Direct Recycle Technology.” This is a newly developed method of turning pieces of used PET-bottle flakes directly into preforms, which are intermediate products that look similar to test tubes, that will later be blow molded into PET bottles.
The conventional way of making preform from flakes involved a process of heating and melting the flakes, crystalizing them and then melting the crystalized pellets again before injecting them into the molds of the preform.
The reason behind the seemingly meaningless process of heating the material twice was because there were two separate machines — one that heats and melts flakes into crystallized pellets and the other that melts the pellets again to make preforms.
Munehiko Takada, chief specialist of the Packaging Material Department at Suntory Monozukuri Expert Ltd., explained that, “The temperature has to go up to about 300 degrees to melt the material, so it is a major reduction of carbon emissions that we were able to make one machine that does everything, skipping unnecessary steps.”
This new technology is said to reduce carbon dioxide emissions by 25 percent compared to mechanical recycling. This contributes to a more than 60 percent reduction in carbon dioxide emissions compared to petroleum-derived PET.
Four companies, Suntory, Kyoei Industry Co. from Japan, Sipa SpA of Italy and EREMA Group GmbH of Austria, collaborated in creating a machine that combines the two processes enabling a shortcut from “flake to preform.”
With this new technology, recycling PET bottles has become more efficient and environmentally friendly. However, recycled PET cannot replace the entirety of PET bottles since not all of them are collected or clean enough to be recycled. The quality of the material — for example, color and viscosity — also changes depending on how many times it has been recycled.
New PET needs to be brought into the recycling cycle to maintain a balance in the quality of materials; Suntory remains dedicated to realizing this environmentally friendly balance.
In 2012, it launched a collaboration with American venture capital firm Anellotech Inc. to make sustainable PET material from wood chips.
Suntory has been investing in Anellotech, which has built a testing plant in Texas, in a bid to introduce the bio-based PET into the recycling cycle to eventually replace all petroleum-based PET. This will not only make the products and the production process greener, but also minimize the impact of oil price fluctuations.
“We have just started to work on research to make PET from waste plastics that are not originally made from PET. As a global company, we will accelerate our efforts with high aspirations to demonstrate good practices that are both environmentally and economically sustainable,” Niinami said.